The Recreational Craft Directive, which is part of European law, entered into force on 16th June 1998. In Europe, this directive applies to most yachts between 2.5 metres and 24 metres in length and the builder of the craft is responsible for ensuring that it meets the requirements of the Directive.
Within the RCD, the Standard that applies to seacocks and through-hull fittings is ISO 9093-1. This Standard states that materials used “shall be corrosion-resistant or shall have protection against corrosion”. It also says that the “material used for the fitting which, within a service life of five years, does not display any defect that will impair tightness, strength or function”.
The fitting shown in Figure 1 shows a failed hose-tail that joined the engine cooling intake hose to the elbow joint & seacock on a 34’ sailing yacht. The Beneteau Oceanis 34 was just over five years old when the survey took place.
Just prior to the failure of the hose-tail, the engine had happily propelled the vessel during a 30 minute sea trial of the engine, most of which was spent running at high load. It was during the following survey inspection that the defect was discovered: As part of the survey of any yacht, the surveyor will aggressively test the hose clips, hoses, valves and skin fittings, looking for evidence of corrosion or decay. The first thing that I did with the assembly was to close the valve, just in case anything broke during the following inspection. A few light taps with a small hammer, with the impacts directed to the bands of the hose clips, resulted in some movement and a small spurt of water coming from the region around the end of the hose. A few more taps with the hammer and the assembly broke in two, as shown in Figure 1. The hammer wasn't wielded in a heavy-handed way, indicating that the hose fitting was very close to failure.

Figure 2 shows the hose-tail after having been removed from the elbow joint and the reinforced hose.
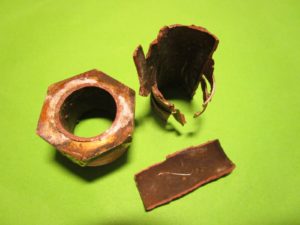
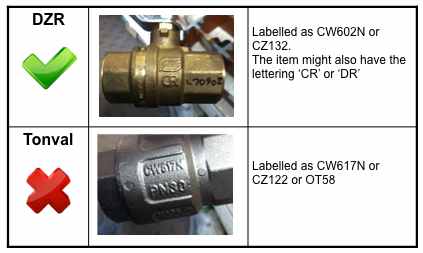
It is usually easy enough to see what grade of brass or bronze the attached valve is made from. DZR brass valves will have the text ‘CR’ embossed on the main unit, or may have CW602N or CZ132 embossed or engraved on the side. DZR valves are acceptable, but Tonval is certainly not good for skin fittings & valves located near to or below the waterline. Tonval fittings will have CW617N or CZ122 embossed on the valves. If you have any valves on your craft that are made from Tonval, consider replacing them as soon as practicable.
Identifying the material of a valve may be straight forward, but hose-tails like the one shown in Figure 2 are a different matter. There’s not much space for the manufacturer to emboss or engrave any sort of identification label. Take a look on the shelves of most chandleries. Loosely packaged items are often un-labelled and there’s a risk of mixing up bronze, DZR or Tonval fittings. Many of the larger online chandleries only offer these hose-tails in ‘brass’, so it’s not even made clear what grade of material they are made from.
When replacing the skin fittings on your GRP boat, or if fitting new ones, use phosphor bronze fittings if possible. If you’re looking for something cheaper, make sure that you don’t get any Tonval or domestic plumbing brass mixed up with DZR. If the valves & fittings on your chandler’s shelves are vacuum packed onto printed cardboard, make sure that they’re labelled ‘DZR’ or have 'CR' embossed on the valve body. Tonval contains 40% zinc. This leaches out of the brass, leaving a very pink coloured and very porous copper behind. Some people describe the colour as ‘caroty’, which equally describes the strength of the remaining material. Too often, this ‘caroty’ colour can’t be seen until the hose-tail or valve breaks off.
A sensible, low maintenance alternative to metallic items are the glass-reinforced nylon valves & skin fittings made by Tru Design, Forespar (Marelon) and others. However, the strength & reliability of these valves & skin fittings depends very much on the quality of installation. It's important to use the load-bearing collar otherwise the installation would be very weak in bending, particularly in cold environments. Also, to make sure that the installation is as strong as possible, ensure that the load-bearing collar is bedded down onto a perfectly flat surface that is perpendicular to the axis of the valve. If not, the assembly will be distorted and unduly stressed when the threaded parts are tightened. Thick marine ply that is well sealed with epoxy resin is suitable. This plywood should be bedded down onto the hull surface with a thick epoxy paste.
It's best not to use plastic skin fittings where they might be impacted by pontoons, harbour walls etc as their impact resistance isn't as good as the metallic ones. Plastic ones shouldn't be used in an engine compartment as they won't withstand the temperature of an engine fire.
If you have any questions relating to the metallic skin fittings on your vessel, please contact our Marine Surveyor today.